
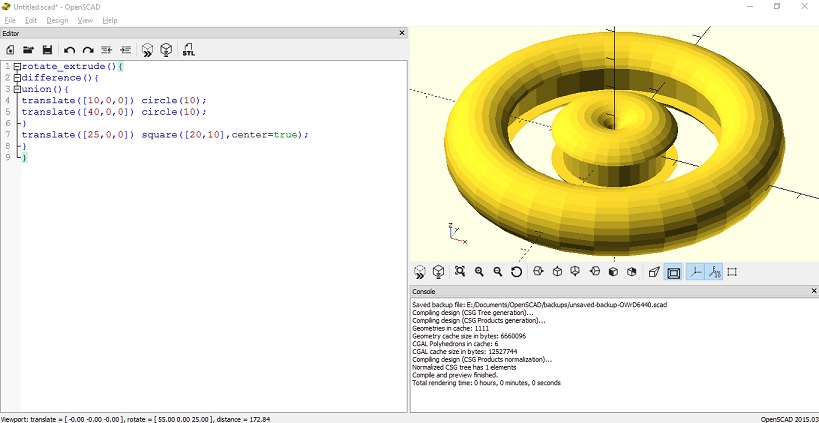
I’ve found both issues (approximate circles and printer accuracy) and the definitely compound each other.
#Openscad 3d printing software
Posted in 3d Printer hacks, Software Hacks Tagged 3d printed, accuracy, goldilocks, openscad, precision, tolerances Post navigation Interested in OpenSCAD? It will run on nearly any hardware, and you can get up and running with the basics in probably less than ten minutes. This concept can be implemented in any number of ways, and OpenSCAD makes a decent option due to its programmatic nature. The array gets printed out, servos are test-fitted to them, and whichever option fits best has its dimensions used for production. That’s exactly what did, using OpenSCAD to generate an array of slightly different sizes and shapes. Therefore, one way around this is to empirically determine which measurements result in a perfect fit, and use those for production on that specific 3D printer. It will be off by some amount, but usually consistently so. A 6.3 mm diameter hole in a CAD model, for example, will not come out as exactly 6.3 mm in a 3D-printed object. What made doing this necessary is the fact that every 3D printer has some variance in how accurately they will reproduce small features and dimensions. By printing one part, could test-fit dozens of options. perceived that to be the case when needing to design and 3D print servo horns that would fit factory servos as closely as possible, and used OpenSCAD to print a “Goldilocks array” from which it was possible to find a perfect match for his printer by making the trial and error process much more efficient. There is something to be said for brute force or trial-and-error approaches to problems, especially when finding a solution has an empirical element to it.
